Work Safety Guide for Meat Processing Workers: Identifying and Addressing Safety Concerns
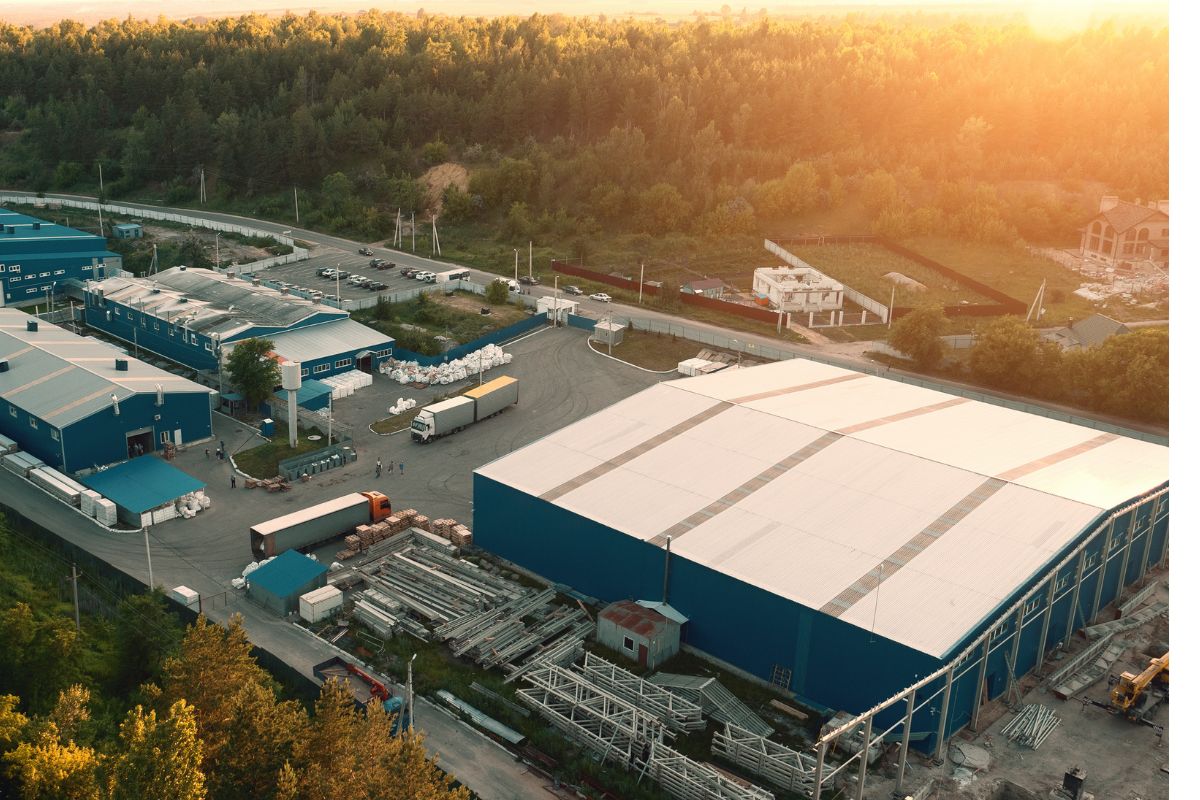
Working within the meat processing industry by its nature carries a high degree of potential hazards which can lead to serious or even fatal accidents.
Recent (2022-2023) engagement by Workplace Health and Safety Queensland (WHSQ) with the meat processing industry has confirmed safety workplace safety is a major concern for abattoir workers in Queensland and an ABC Four Corners investigation in 2022 found Australia's largest meat processor had repeatedly failed to protect its workers from serious injuries.
Despite the undeniable risks involved in the meat processing industry, it's important to understand that employers are bound by law and ethics to ensure a safe working atmosphere for their employees. Recognising and arguing for these rights can significantly contribute to the creation of a safer workplace.
What are the common hazards?
The industry of meat processing has lots of potential safety issues including the following:
- Equipment-Related Hazards: Operating heavy machinery and tools, which are often sharp and powerful, can potentially cause severe injuries if misused or malfunctioning.
- Biological Hazards: Exposure to animal-borne illnesses and diseases is another risk within this industry, posing potential health threats to workers.
- Physical Strain: Repetitive actions, prolonged standing, manual handling and lifting can lead to musculoskeletal disorders over time.
- Cold Working Conditions: The necessity for refrigerated workspaces can pose additional challenges, including the risk of hypothermia or frostbite.
- Chemical Hazards: Handling cleaning agents and certain chemicals used in the meat processing industry can present risks of burns, respiratory issues, and other related health concerns.
Below we cover five steps to avoiding injuries and advocating for safety as a meat processing worker in Queensland.
1: Understanding Your Safety Rights and Employer's Responsibilities
In Queensland's meat processing sector, maintaining a safe working environment is not just a moral obligation, but a legal requirement. This is a shared responsibility. On one hand, workers have distinct rights and should be equipped to identify and report potential workplace hazards effectively. On the other hand, employers are bound by law to ensure their worker's well-being, setting necessary safety measures and consistently adhering to them. When both parties are apprised of their respective responsibilities, it paves the way towards a harmoniously productive and secure work setting.
Employee Rights:
- Right to a safe work environment: It is a fundamental right of every worker to perform their duties in a setting that is free from recognised hazards that can potentially cause harm or death.
- Right to training: Workers should have access to appropriate educational material and on-the-job training to properly manage and mitigate work-related hazards.
- Right to safety equipment: Employees are legally entitled to receive and use personal protective equipment (PPE) and other equipment to help guard them against workplace hazards.
- Right to refuse hazardous work: Workers have the right to refuse work if they believe it to be imminently hazardous, without fear of retaliation or dismissal.
- Right to report: Employees are free and strongly encouraged to report any unsafe working conditions or hazards to either their supervisors or appropriate safety representatives.
Employer Responsibilities:
The employer needs to support all the rights outlined above including creating a safe working environment, providing training and supplying safety equipment.
They also need to ensure the following are done;
- Maintain regular safety monitoring: Regular inspections and safety monitoring should be conducted by the employer to prevent overlooked hazards and to ensure safety measures remain effective. Major fines can be issued where an abattoir owner fails to properly inspect and maintain a plant.
- Establish an effective reporting system: Employers should establish an accessible and easy-to-use reporting system for workers to promptly report any identified workplace hazards or concerns.
Part 2: Recognising Signs of Unsafe Practices
Use bullet points with a sentence to explain each point.
Observation and awareness are critical for identifying unsafe practices in a meat processing environment. Here are a few signs to watch out for:
- Unsafe handling and disposal of hazardous material: If the employees are noticed to be manually handling or discarding materials that could pose a risk, either chemically or biologically, it's a sign of improper procedures in place.
- Poor personal protective equipment (PPE) compliance: Lack of gloves, aprons, goggles, masks, and other protective gear, or the use of damaged or dirty PPE, is a clear sign of a dangerous working environment.
- Insufficient training: Workers who don't appear to be adequately trained for the tasks they are performing, or who seem unsure about safety procedures, could indicate a disregard for employee well-being.
- Improper use of tools and equipment: This can be significant if employees use knives or machinery without appropriate training or without following the prescribed safety measures.
- Unsanitary conditions: A meat processing plant that is not regularly cleaned and maintained could pose significant health risks due to the potential for bacterial and viral contamination.
- Inadequate ventilation: In a meat processing environment, good ventilation is integral to ensure the dispersion of airborne contaminants that can pose a health risk.
- Disregard for physical and mental health: If workers are constantly exposed to excessive noise, harsh lighting, extreme temperatures or pressures to work overtime, the working conditions are unsafe.
Part 3: Effective Communication of Safety Issues
Successfully advocating for a safer workplace relies heavily on your ability to effectively express your concerns. Good communication forms the basis of a proactive approach to workplace safety. The following points offer some guidance on how to communicate your safety concerns effectively:
- Identify the appropriate authority: Usually, your immediate supervisor or safety representative serves as the initial point of contact for safety-related issues. Establishing a good communication channel with them will ensure the speedy resolution of safety concerns.
- Keep a record: Document every safety risk observed meticulously. These records should include dates, times, and specific details regarding the unsafe conditions. It can prove an essential aid when demonstrating the gravity and persistence of safety issues to your supervisor.
- Utilise available resources: Health and safety notice boards or suggestion boxes are often available in most workplaces. Use these tools to voice your concerns and proposed improvements for safety protocols.
- Participate actively in safety events: Engage in safety meetings, inspections, and training sessions, as these are prime moments to voice safety concerns. Always aim to express your views clearly, constructively, and respectfully. This shows a commitment to improving the safety conditions in the plant and helps enlist others' support.
Part 4: Collaborative Problem-Solving
In the pursuit of creating a safer working environment in Queensland's meat processing plants, collaborative problem-solving plays an essential role. Measures that workers can undertake include:
- Working Collaboratively: Actively engage with your colleagues, supervisors, and health and safety representatives to identify potential safety issues and develop appropriate measures. Remember, safety depends not just on an individual's actions but on a collective effort.
- Attending Training Sessions: Make the most of any available training sessions designed to enhance workplace safety. These programs might include guidelines on operating potentially dangerous equipment, conducting risk assessments of the workplace, and best practices for personal protective equipment. Being receptive to such training can imbue workers with the knowledge, skills, and attitudes necessary for maintaining safety standards.
- Sharing Successful Strategies: If you or your team have implemented a successful safety strategy in your workplace, consider sharing it with your peers. Such exchange of ideas can stimulate a proactive safety culture within the meat processing industry, wherein everyone takes responsibility for their safety and the safety of those around them.
- In summary, the safety in the workplace cannot be the sole responsibility of either the employer or the employee; it ensures a cooperative relationship among all stakeholders. By actively engaging in ongoing training and sharing best practices for workplace safety, workers can play a pivotal role in upholding high safety standards in Queensland's meat processing industry.
Securing Further Assistance
In circumstances where you feel your concerns about workplace safety have not been given the serious attention they merit, or if you believe your rights as a worker in Queensland's meat processing plants are being overlooked, there are further actions that can be taken. Herein are some steps you might consider to ensure your rights are upheld, and your work environment remains on par with safety regulations:
- Contacting Senior Management: If your immediate supervisor or manager does not adequately address your safety concerns, it may be necessary to escalate the issue to higher management levels. They often have more authority and resources to implement needed changes.
- WorkCover Queensland: This is an external body that could become involved if the employer is not taking your concerns seriously or abiding by safety regulations. WorkCover Queensland is well-positioned to oversee workplace safety, and they have the authority to penalise businesses who disregard safety laws. Simply visit their website, or call them to lodge a complaint.
- Formal complaint: Filing a formal complaint is often the subsequent step if all else fails. A complaint can be filed with Workplace Health and Safety Queensland, which will then conduct an investigation of the situation. This is especially vital if there is an imminent threat to your safety or that of your colleagues.
- Protection against Unfair Treatment: As a worker, you are protected by laws against any form of retaliation from your employer for voicing safety concerns or reporting safety breaches. The Fair Work Commission provides mechanisms to report and handle such instances of unfair treatment, ensuring your rights and job stability are preserved.
In conclusion, understanding and advocating for your safety rights in Queensland's meat processing plants is an essential component to a safe and healthy working environment. By being aware of your entitlements and your employer's obligations, you can help foster a workplace that prioritises safety and adheres to the pertinent legislation.
Safety in the workplace is not just a mere requirement; it's a moral and legal commitment to protect people's lives and reduce accidents in the workplace. Remember, it's your right, protect it.
If it's time to talk, we're here to help. Get free advice direct from our solicitors today.
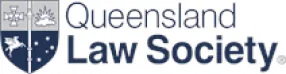
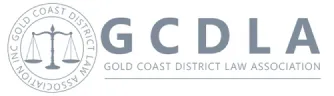
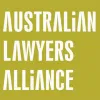
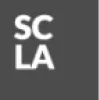